Case Study
US Postal ServiceSummary
This study involves training within the US Postal Service which has many departments that are subject to strain, sprain injuries. However, the three departments included here are Customer Service which is involved in the sorting and delivery of mail, Plant Operations which involve the processing and distribution of mail to the various Post Offices and Vehicle Maintenance. The total USPS facilities trained with PowerLift is approximately 210 in number. These facilities were gradually trained over the course of years and during that time 14 were followed statistically, comparing the number of strain, sprain injuries the year before training to the year after training. The results varied from 100% reduction in injuries to a 17% reduction. The telling statistic was the average reduction however and it was 69%. But what about the 17% reduction?
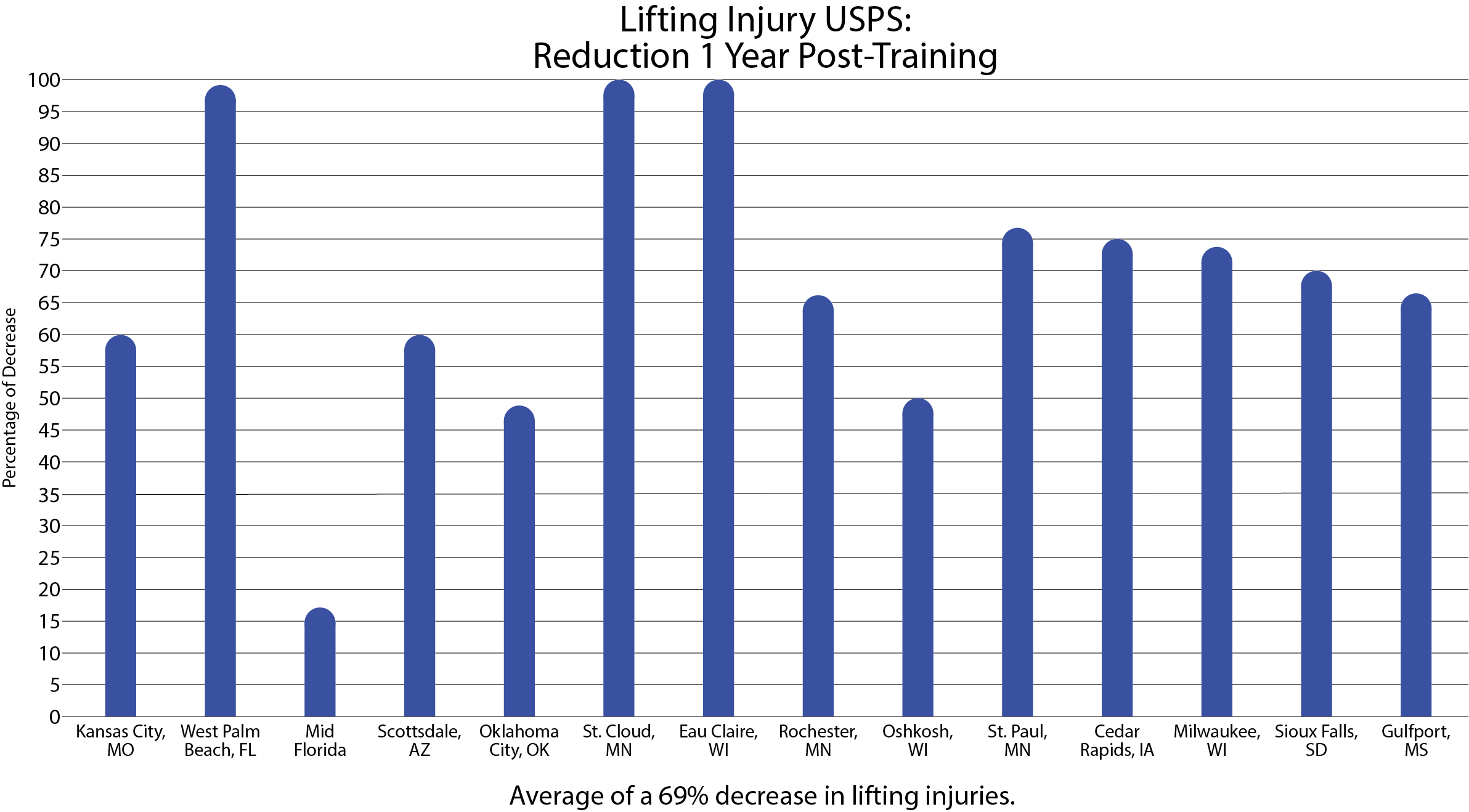
Notwithstanding the fact that that particular plant was aiming for a 3-4% decrease in lifting injuries this seems too low to us when compared to the other 13 facilities. We have found over the years that with any type of organization, you get out in terms of good reductions in injury, in direct proportion to the effort that was put in. Low achievers in our experience are those who show a video once each year and expect to see positive results for nearly no effort. The effort required is explained below.
METHOD
Initial training was rolled out as a Train-the-Trainer initiative followed by a series of craft employee classes presented by a non-postal, certified PowerLift trainer. Not all employees were trained by the non-postal trainer however, with the balance of employees being trained by the now certified USPS PowerLift trainers.
Prior to any training of the USPS, all of the tasks performed by postal craft workers was documented and videos as well as PowerLift Safety Talks were created showing in detail how to use PowerLift for those tasks. Indeed, it was found that the tasks performed by postal craft employees are a perfect fit for PowerLift technique. It is almost that PowerLift was conceived just for the postal service. After the initial training the DVD video shorts and Safety Talks were used as safety briefings on a regular basis in an effort to both remind the employees to use PowerLift and to create a material handling safety culture based on it. The result was a change in work behaviors that is so necessary to reduce risk of injury. As a result, craft employees embraced the training and were actually quite relieved to receive a training protocol that actually works in real life. One element of the training that contributed greatly to their acceptance of the training was that they found, contrary to initial beliefs, the techniques do not take any extra time to use and in fact, actually made some tasks fast and much easier to perform.
One to two team members held classroom sessions that were composed of five to ten order selectors who were introduced to five different PowerLift® techniques of lifting, pushing and pulling. Following the classroom instruction the selectors were taken to the production floor for hands-on practice at the pick slots. The initial reaction of the selectors was that the techniques shown would take too much time to accomplish and that they would not be able to keep up with their pick rate. In fact, it was found out as they became more proficient with the tasks, that the pick rate was not affected at all and resulted in less fatigue because of the inherent efficiency of the technique.
The company also renewed its effort at making safety a much more important part of the job with PowerLift® at its core. Safety awareness continues to be a priority and is supported by weekly Safety Talk presentations, observation of employee work practices and the immediate training of new employees in the PowerLift® techniques of order selection.