3 Pillars of Material Handling Safety for a Breakthrough 2020
We at PowerLift® acknowledge and commend you for your commitment to creating and maintaining the safest workplace possible for yourself, your employees and your company. Whether you and your organization are successful in realizing and fulfilling your commitment, or you are experiencing challenges and barriers to a workplace with safe material handling practices, we invite you to consider what is possible when you embrace these 3 pillars of safe material handling.
Pillar #1: Training, Training, Training.
Material Handling Training is crucial to the ongoing safety of your workers. But we’re not talking about a one-and-done program. Programs, by nature, have a temporary impact. Rather, we’re referring to an effective material handling training system: one which causes a fundamental shift in the culture of the organization. Any training system you adopt and utilize must be…
… Training that sticks.
Most safety programs fail to address one very human tendency: the phenomenon of habit. Training is only effective when trainees alter their conditioned responses and behaviors over time. And that, in turn, is only possible when the environment in which the trainees operate calls for – and reinforces – the newly-learned behavior. PowerLift® Training employs a system called “Train-the-Trainer.” The process is simple: train an initial group of employees selected from all levels of an organization. Upon successful completion of the training, members of this initial group become the trainers and peer-coaches for other workers. When an old habit surfaces, as they do (because, you know, Humans), the peer-coach addresses the issue immediately, discussing safer and more effective ways to perform the task. Training is on-going in the form of over 1200 individual, fully illustrated single-page guides. These cover hundreds of activities, customized to your industry, and can be posted throughout the workplace. In addition, PowerLift® Training includes weekly safety talks, where workers come together for a few minutes to discuss and resolve material handling challenges as a community, further reinforcing the training, and strengthening the community and safety culture within your organization. Over time, workers develop new lifting habits that can reduce injuries by as much as 90%.
… Training that works.
A training system such as PowerLift® Training works in concert with the mechanics and physics of the human body. Unlike the commonly-used ‘squat-lift’ (which suggests a stance that is 12 inches to shoulder-width) Powerlift® teaches your employees to lift with a wide stance for stability and power. In addition, PowerLift® Training eases the stress on lifters’ knees by keeping knee-bends to just 100°. This has the advantage of bringing the body over the load. More power is therefore available for lifting since balance is no longer as much of an issue. Workers who are older or overweight also benefit because they are able to carry out the lift more effectively, and with a greatly reduced risk of injury.
… Training that empowers leaders.
The more you build and empower a community of leaders who share your commitment to a safe workplace, the closer you come to creating a workplace where safety is baked into the culture. And let’s be honest: safety managers wear many hats. Empowering your employees to be responsible for their own safety, and the safety of their peers provides you with a win-win situation that fulfills your commitment to material handling safety.
PowerLift® Training capitalizes on our natural human tendency to socialize. A large part of that tendency is our curiosity, together with our natural desire to ‘show and tell.’ We love to discover and share information with each other. And when that tendency is applied to the workplace and prevents injury to the individuals in our workforce, everyone wins.
Pillar #2: Monitor, Measure, and Monitor Again.
Knowledge is power. And, to ensure that your employees are safe from injury, you need to know (at minimum):
- Who is taking actions or engaging in behaviors that work? Who is not?
- Where are your injury ‘hotspots’?
- Are your employees utilizing the safety training effectively?
This pillar has 2 basic components, and they are part of a new wave of safety equipment that combines wearable technology with artificial intelligence and machine learning and takes the guesswork out of injury prevention.
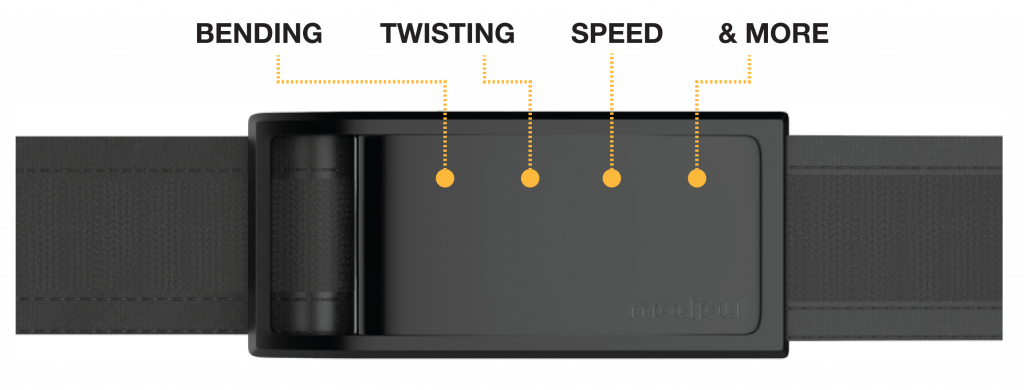
The SmartBelt by Modjoul™ consists of a belt that is equipped with 8 sensors and GPS. It is capable of sensing and identifying the activities of the employee throughout the day, like sitting and standing, walking, running and driving, as well as lifting, reaching and stretching. The built-in accelerometer can also detect tripping and falling. Other sensors provide environmental data, such as temperature and humidity. The collected data is stored and transmitted via wifi to a protected database where it is organized and classified according to user-defined parameters. Users can then access the resulting reports on any mobile device through one of three different dashboards: CEO, Supervisor, and Employee. The organization determines the level of access to the information.
With the knowledge and information provided by Modjoul™’s SmartBelt, you can determine:
- Where the training has been most effective (and for whom), and where it is lacking.
- The physical location(s) that put your employees at the highest risk of injury. Identifying the ‘hotspots’ empowers you to mitigate, or even eliminate the potential danger.
- The specific training that is needed (and for whom): you can allocate resources more efficiently.
SmartBelt also provides ongoing monitoring, further extending your ability to protect your employees over time.
Modjoul™’s SmartBelt is, by itself predictive and preventive: when selected and activated, the haptic feedback system vibrates when the belt detects behaviors, actions or motions that are potentially dangerous, effectively warning the user that danger could be imminent. The user is then able to stop the risky behavior or action, preventing injury.
Pillar #3: Empower, Engage, Encourage.
Who owns material handling safety at your organization? If the answer is “management” or “the administration,” it’s almost certain that the effectiveness of any safety training is severely compromised. In a “top-down” safety culture, workers will experience any training as being ‘done to’ them. Safety becomes a ‘management thing’ to be checked off to satisfy a standard. Who’s left out? Your worker.
In reality, the safety of your workers belongs squarely in their hands. It is their health and well-being that is at stake. When every employee is empowered to take ownership of their own safety, safe material handling becomes everyone’s business, and they are more likely to engage in (and buy into) the kind of training that works for them. Consider that PowerLift® engages your workers in the practice of safe and effective behavior, both on and off the job. And effective monitoring through Modjoul™’s SmartBelt encourages accountability throughout your workforce. Combining PowerLift® with the power of SmartBelt empowers and encourages awareness, helping you to create and maintain a culture of safety at your organization.
We’re here to support your commitment to a safe workplace.
Let us know how we can work with you to make 2020 a breakthrough year in safe material handling for you. For further information, please visit https://powerlifttraining.com/programs/
Recent Comments