“Culture is a living thing, powered by, and kept up to date by the people who are encouraged to be, in a meaningful way, part of it.” Micah Taylor, Forbes
Peggy, whom we quoted in an earlier post, said that her success is the product of 3 years of training, review, and ongoing participation of her operations and line employees in safe material handling training systems. It took an intentional and concerted effort, combined with a strategy and plan. And it took time.
Patience and commitment to a culture that invests in safe material handling is key to impacting the culture of a company. Once again, a ‘one-and-done’ program approach is ineffective. It bears repeating that programs are temporary in nature. And the tendency for most people is to go back to habits that are familiar, undermining any benefit that a program might have had.
An effective safety culture is one that is self-sustaining. A good place to start is with new hires. Incorporate safety training into the orientation or initial training of every new employee. As new hires are trained, and as they practice the safe-lifting techniques they learn, their training becomes ‘baked’ into their experience of the company. It becomes a case of ‘that’s just how it’s done at my workplace.’ Couple the training with that of existing employees and the peer-mentor structure discussed previously, and you begin to have an effective, lasting impact on the safety culture of your organization.
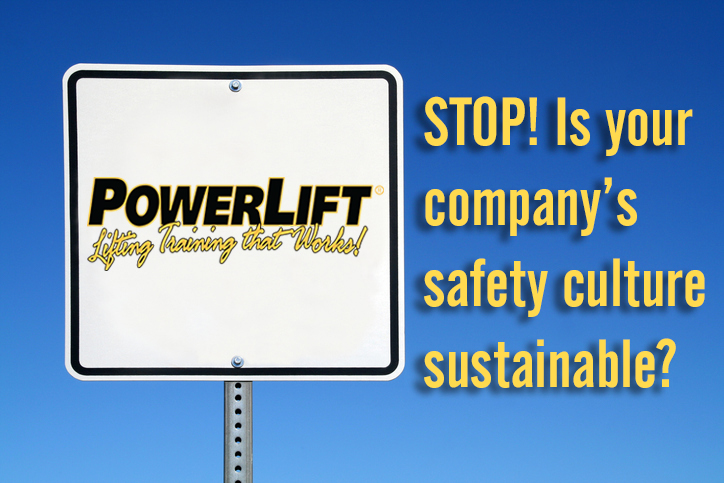
As new hires move up through the ranks and take on greater levels of leadership, they represent the training system and affect their work environment at each level, further establishing and reinforcing safety as a value for all employees. These staff members also serve as mentors for newer, more junior employees. Eventually, an employee who was once a new hire will become a team leader, supervisor, or area manager. The safety culture, now an integral part of the individual’s company identity, manifests itself in every interaction with their employees and with their peers.
A directed, deliberate effort to reinforce the training is also part of creating a culture. Periodically and frequently review the training with your employees. This can be done with minimal disruption: for instance, you can hold 5-minute Safety Talks at the beginning of each shift, and allow different peer-trainers to lead each session. Reviewing safe lifting techniques periodically serves to strengthen good habits. For instance, if you hold a review once every 2 weeks, have different employees demonstrate the correct lifting methods that they use on a daily basis. In addition, debrief the employees regularly: have them share what works and what does not work regarding the lifting methods they employ. From the standpoint of health and safety, reinforce what works, and correct what does not work. Hold a monthly audit with your employees, focusing specifically on effective and efficient ways to lift. This would mean having employees demonstrate the correct lifting methods that they might use to accomplish a task. This is also an additional opportunity to correct what does not work. Although it seems like this takes time and attention away from the work that needs to be done, it actually is an insignificant amount. Peggy reports that a 5-minute safety talk a the beginning of each shift, and a 20 minute-audit a month serves to achieve her results of 1 injury over the past 6 months. While she initially faced some resistance to the safety talks and the audits, she now finds that employers and managers are eager to have them and that the safety talks and audits increase the level of job satisfaction and productivity.
Baking safe material handling into the culture of a company also means celebrating the good news. Over time, as favorable results accumulate, acknowledge the employees for the outcome of adhering to the safe material handling system. Highlight the training, and the differences it has made to date. Allow employees to share results from outside the workplace if any. Safe material handling technique is not just limited to the workplace, but also at home.
PowerLift helps companies create a lasting safety culture that will improve the environment in such a way that it can actually positively affect peoples lives. PowerLift can be the foundation of your companies new safety culture or it can be a great addition to an already existing one. Learn more about how the PowerLift training system can improve your company’s safety today.
Click here to see the next post of this 5 part series.
Click here to see the previous post of this 5 part series.
Recent Comments