It’s a twist on a well-worn topic. But we wanted to catch your attention. And we’re shameless.
Many of us have already heard enough about workplace safety to cause us to roll our eyes.
Again.
So here’s a different crack at the topic of workplace safety. Maybe you’ve encountered these attitudes before. Or maybe you’re someone for whom one of the following is, in fact, a closet attitude. Or maybe one or more (or all) of these attitudes are alive and well at your place of work. And it can be anyone in the company: administrators, managers, supervisors, and workers; no one is exempt or excepted.
Because – regardless of rank – if anyone acts on a single one of these attitudes are present, it can be a step in the direction toward disaster: for the worker, for the department, and even for the organization as a whole. Because no matter how you approach it, workplace injuries cost. A lot. And many of those injuries have their roots in one of the following 3 attitudes.
Attitude #1: Only Losers Ask for Help.
What has us embrace an attitude like this one? Is it Pride? Or is it its equally dangerous opposite: Shame? Whatever lies at the heart of this attitude, the potential for disaster is huge. What’s especially tragic is that not asking for help can be a major contributor to the $1B cost of workplace injuries in the US every year.
The truth of the matter is that a human being’s musculoskeletal structure is designed to handle certain loads. Go beyond those limits, and injury is inevitable. Resistance and endurance training can extend those limits, but it takes time to develop. And, each individual is unique, with their own limits. The sad thing? These kinds of injuries are almost completely preventable, and therefore completely unnecessary. Knowing – and accepting – the limits of our capabilities are highly effective in injury prevention. And once we’re clear that superpowers are best left in the world of entertainment, we can then work as a team to accomplish what needs to be done.
PowerLift® Training empowers employees to recognize when to request assistance with moving or lifting a load. In addition, PowerLift® promotes a peer-coaching approach to material handling. This means that no one needs to carry the load alone. Problem-solving becomes a team effort, and a team win.
Attitude #2: Don’t Tell Me What to Do (or How to Do It)!!
See Attitude #1, re: Pride. We’ve probably all met (or worked with) that fellow employee. You know, the one who always knows better. The one who resists any advice or suggestion, and who will take offense if you so much as try to tell them anything. This, too, is an attitude with a single destination: potential injury. In this case, it’s merely a matter of time before the inevitable Workers’ Compensation claim. In most cases, this attitude also comes with a complete lack of responsibility; to the possessor of this attitude, life is simplified: it’s almost always someone else’s fault.
One way to overcome this attitude is to make safety a team effort, and create a culture of safety within the organization. PowerLift® accomplishes this by training individuals from various levels of the organization and then working through those individuals to train the rest of the workforce. These individuals become safety coaches, in what is known as “Train-the-Trainer.” In an environment where peer-coaching is the norm, individuals are more likely to look out for each other and offer safer or healthier alternatives when fulfilling a task. With best material handling practices ingrained in the culture of the enterprise, this attitude cannot thrive.
Attitude #3: We’ve Always Done It Like This/We’ve Never Done It Like That
And how many trips to the ER will it take before we change how we do something? It’s no secret that tradition and a safety-conscious culture are not always the best of friends. In fact, they often run counter to each other. Sometimes it’s even the workspace itself. While the workers themselves may be doing all they can to work safely, the work environment in which they find themselves may be inherently, and unnecessarily, risky. And change doesn’t come easily; nor does it come cheaply. Sometimes, unfortunately, tradition wins until the company is forced to change either by legislation or by economic forces. Where traditional practices can be altered, the pathway to a safe and effective safety training system could have 2 approaches.
- New techniques, technologies, or methods.
Our star exhibit is the time-honored squat-lift. PowerLift® Training shows that the squat-lift is simply not the best way to handle materials. The squat lift diverts physical power from material handling to balance, reducing what’s available to safely move a load. PowerLift® techniques teach people to use the mechanics and physics of the human body’s construction effectively. This translates to a more efficient use of energy, and greater power available to accomplish the tasks at hand. PowerLift® has also teamed up with Modjoul™, creators of SmartBelt. This wearable technology monitors the wearers’ movements and behaviors for safety. The data is stored and made available upon demand to track how safely individuals are performing their tasks. Behaviors can then be reinforced or corrected to improve safe practices in the workforce. PowerLift® and SmartBelt work together seamlessly to reduce workplace injuries dramatically.
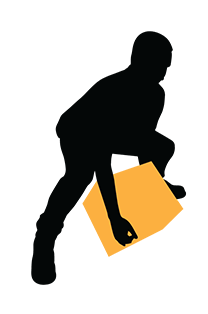
- Redesigning the workflow/workspace
With the advent of PowerLift® and Modjoul™, organizations can also monitor and evaluate environmental conditions. If several, or all, individuals within a team experience the same issue at a specific workstation, the company can then make informed and focused adjustments to the problem area. This has the added bonus of boosting productivity while also making sure that the safety of the workforce is uncompromised.
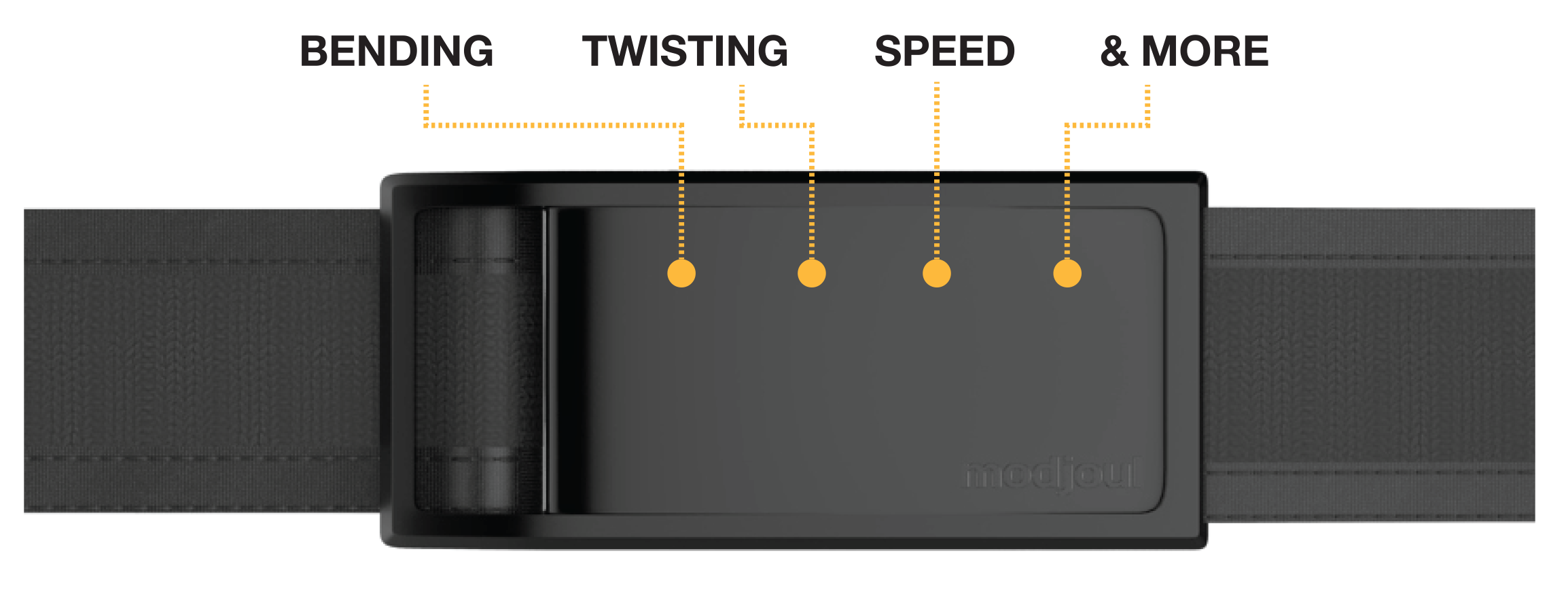
Have you encountered these attitudes on your production floor? Or perhaps you’ve experienced a situation where PowerLift® Training and the Modjoul™ SmartBelt would make a significant difference. Please let us know how we can positively impact the safety of your workplace.
Recent Comments