Let’s face it: there exists in most companies, an “us against them” mindset between operations and corporate levels. Which means that, if corporate hands down a safety training program, it won’t stick. Because the average worker will feel like the training is being done to them. There’s an innate human resistance to being dominated by them, whoever ‘them’ happens to be. A safety training program that is being imposed by the corporate levels of manage-ment will certainly be experienced as a form of domination from “them.” Says Peggy, whom we quoted in an earlier blog post, “if it comes from Corporate, the program has no chance. If it comes from the Safety Department, forget it. No one will do it.”
The solution? Train the trainer ( peer training ). Offer the safety training to a “first wave” of employees from all levels of the company. Include line operators, team leads, supervisors, and even various levels of management.
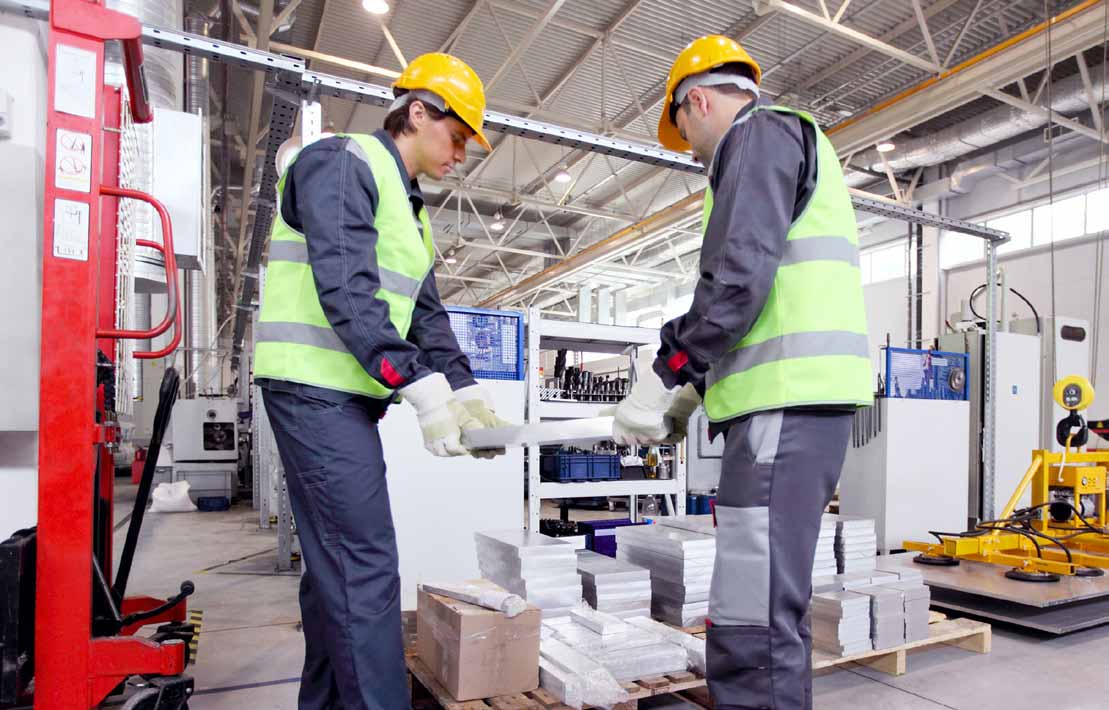
Upon completing the training, these people become your safety trainers, coaches, and mentors to their peers. As their co-workers see a positive difference that safe-lifting techniques make, adoption is likely and effective in both the short- and long term. What starts as a safe-lifting training becomes a safe-lifting habit. In the meantime, schedule the training for each operational employee and make it clear that everyone will, at some point, participate in the training as part of their job. Most importantly, make it known that each employee has the support of their peers to ensure their success. Peer-to-peer training succeeds where corporate-to-operational training fails. Operational staff responds to each other far more readily than to someone who is perceived as distant or disengaged.
“The best trainers are those who have had a back injury. Because they know what it’s like to feel the effects, and the benefits of avoiding them,” says Kevin, Ergonomics Manager for an international heating and cooling corporation for over 15 years. “When management and their employees are both engaged in safety concerns, those concerns are brought to light. Then we can work on maximizing efficiency and minimizing injury. [Safety is] no longer a priority. It’s a value.” – PowerLift Client
PowerLift’s unique peer-to-peer training style of material handling safety training gives companies the opportunity to build on their existing safety culture or to be the foundation of a new one. Safety training is better received if it is presented to the trainees by someone they know and work with on a day-to-day basis. When your trainers are a constant fixture at your facility the margin for success grows exponentially.
Click here to see the previous post of this 5 part series.
Click here to see the next post of this 5 part series.
Recent Comments