When considering workplace safety, it is vitally important to answer a set of questions:
- Is it the worker, or is it the actual work (or both) that presents a safety challenge?
- How could we find out?
- Once we know the answer, what do we do?
This post is not about playing the blame game. That’s a topic for a future post.
To answer the first question, we must answer the second. How will we know if it’s worker or work that bears the greater responsibility for workplace injury? The solution is deceptively simple: measure it.
Because if you don’t measure it, you can’t manage it. There needs to be a way to monitor and track the frequency of correct versus incorrect safety practices and behaviors in any given location at the place of employment.
Consider this: If poor behaviors are only present in one or two employees, then we know that these employees are outliers: they are exceptions rather than the rule. Corrective measures can then be implemented to protect these workers
But what if poor – and potentially detrimental – behaviors are showing up in a large number of workers in a given location? Then the data raises some questions, such as: what are workers expected to do as part of their job? Or, are workers required to interact with their environment in a way that could be ultimately injurious to them? In either case, it may be necessary to make adjustments that will protect the workers while on site.
Now we address the monitoring/measuring itself. Any method of monitoring and measurement must be:
- Unobtrusive. It would need to fit into the daily workflow without obstructing the worker. It might even be wearable technology.
- Able to differentiate between behaviors that are normal to the job, and behaviors that present potential issues… in other words, smart technology.
- Able to establish a baseline, against which specific behaviors are measured.
- Empowering. Ideally, monitoring and measurement would not feel like the safety police are breathing down our necks, watching and waiting to pounce on the slightest infraction.
Here’s the good news. The technology is not only here, but it’s been tested, and proven. And it hits all the right notes. Its’ smart, wearable technology that not only measures what the worker is doing, but what the environment requires the worker to do. And it warns the worker when an activity is potentially dangerous. It’s called the SmartBelt, by Modjoul.
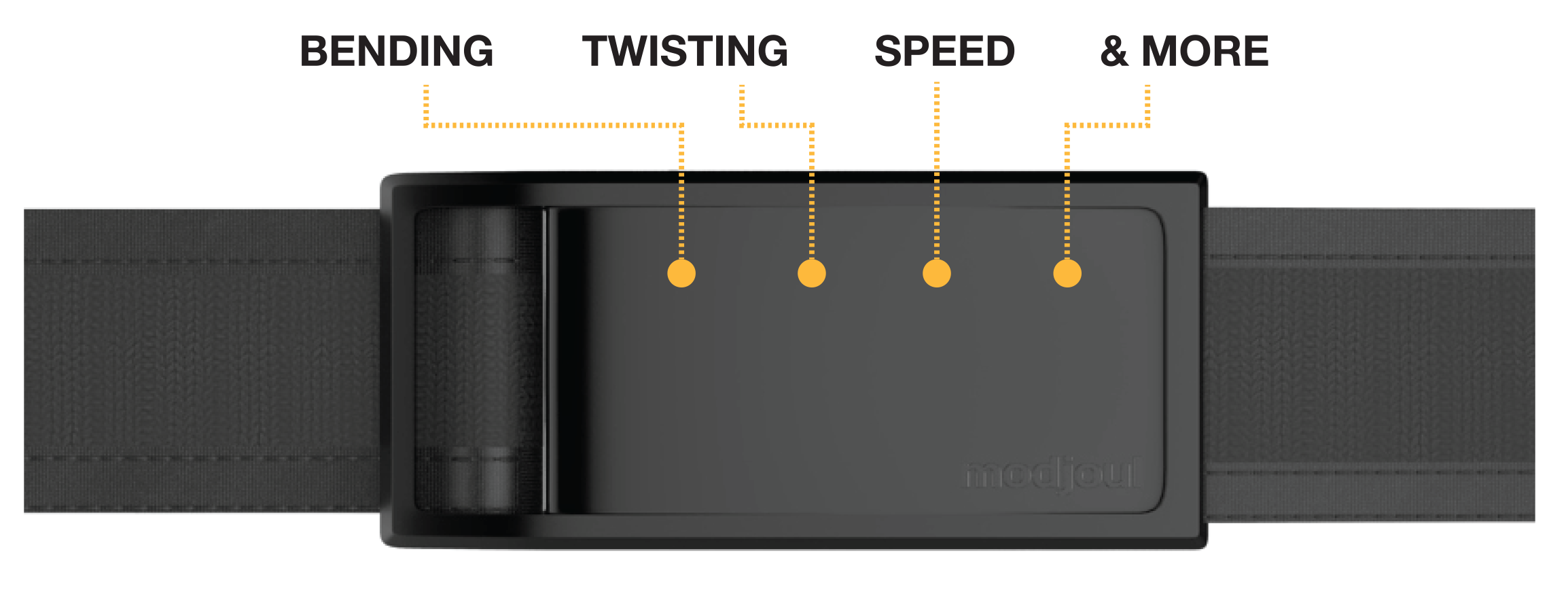

Modjoul’s SmartBelt is, as its name suggests, a belt. The system supports supervisors and management to identify both unhealthy practices and environmental problem areas. SmartBelt measures how workers are performing their tasks. First, a baseline for a given task is established. When occasional behaviors show up as outliers against that baseline, we can safely say that the issue is with the individual worker(s). But then, if many workers are doing the same task, and their behavior is observed to be potentially risky, we can identify that it’s probably the work environment that needs to be adjusted in some way.
So we now know that we can measure and monitor the safe actions and movements of employees. Now what?
Well, whether the risk lies with the worker or the work, the actual solution may require some creativity. Often, it’s as much an ergonomic approach as it is a matter of training. Once a safety issue with a specific location is identified, the remainder of the solution could be simple. Whatever the solution, it does not need to be either complicated or expensive. For instance, adding a platform on a lift provides the worker with adequate footing, reducing the danger of falls, and increasing the muscle-power required to perform certain tasks. Here’s another example: altering the standing height of a worker by a few inches may reduce unnecessary bending or reaching, thereby reducing the risk of musculoskeletal injuries. Voila! Risky situation mitigated – and possibly completely prevented. Considering how much a long-term workers’ compensation claim can cost, the price tag on preventive measures is much more attractive.
Where the solution involves training employees, implementing a safe material handling system like PowerLift Training further improves the odds against accidents and injuries. Safe material handling training like PowerLift provides an effective layer of protection against potentially injury-inducing movements and actions.
Here’s the honest truth: there is no such thing as an inexpensive workplace injury. Because the costs are not just in dollars and cents. It needs to be said: a workplace injury impacts well-being, mental health, relationships and lives. The 2-prong approach offered by Modjoul’s SmartBelt and PowerLift Training equates to a dynamic duo that will defend your company against the spectre of workplace injury.
Recent Comments